The Studio System™
Easy-Adopt Powderless Metal 3D Printing
Built for the Office, Studio, or Lab
Easy, Safe, Cost-Effective Metal 3D Printing
Easy-to-adopt two step process designed for hands-on use with minimal training and runs with little operator intervention.
Desktop Metal’s print and sinter process, combined with next-generation Separable Supports™ and a software-controlled workflow, makes metal 3D printing simpler than ever.
From prototyping to tooling or batch production of end-use parts, the Studio System makes the benefits of metal 3D printing accessible in any office, studio, or lab setting.
Making metal parts is as easy as 1,2
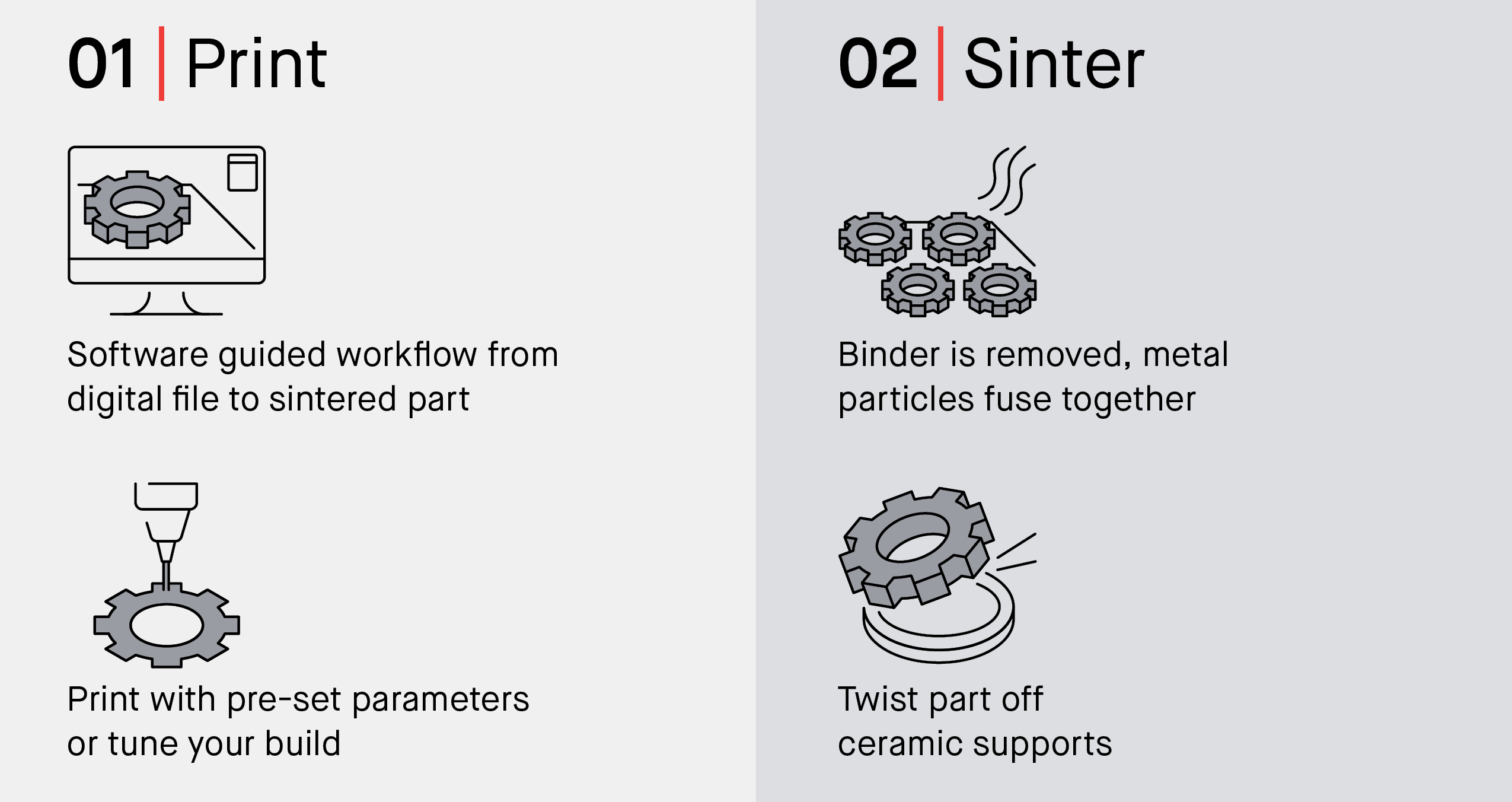
Interested in getting started?
Reach out to our team for a quote on the Studio System.
Safe, Powderless Metal 3D Printing
The Studio System Bound Metal Deposition (BMD) technology uses safe-to-handle metal rods of pre-bound metal powders and polymer binders that are extruded layer-by-layer into complex shapes.
- No loose powder
- No lasers
- No special facility requirements
The perfect solution for any university, manufacturer, or design lab, looking to get started with metal 3D printing.
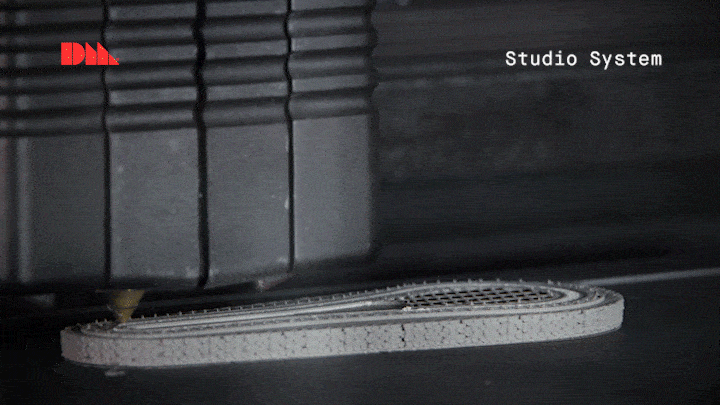
Simplified Metal Part Production
With no solvents, loose metal powder, or lasers, the Studio System is designed for hands-on use with minimal training and runs with little operator intervention. From prototyping to tooling or batch production of end-use parts, the Studio System makes the benefits of metal 3D printing accessible in any office, studio, or lab setting.
-
Complete, turnkey solution
Contains all the equipment you need to begin 3D printing metal parts with user-friendly hardware, feedstock, and an intuitive user interface. Designed to be the easiest approach to sintering, the included Desktop Metal Furnace features a large capacity, advanced graphite retort design and low gas consumption for reduced operating costs.
-
Powder-less metal parts
Safe-to-handle metal rods of pre-bound metal powder and polymer binders, using a formulation similar to the mixture used in Metal Injection Molding (MIM), are available in a variety of alloys. Designed for multi-material compatibility and effortless changeovers with easy-to-swap material cartridges that allow for fast changes without cross contamination or powder-handling requirements.
-
Software-controlled process
Live Studio™ provides an intuitive guide throughout the entire metal 3D printing workflow. From simplified model prep to automated sintering cycles and job queueing, the software applies knowledge from world-leading materials scientists and additive manufacturing experts to automate and optimize the fabrication of high-quality metal parts.
-
Separable Supports
Our next-generation Separable Supports enable greater design freedom and allow for easy post-processing of complex shapes. Software-generated support structures with strategic seams via a ceramic release layer can be broken away by hand after sintering with no cutting tools required.
3D Print Nine Qualified Materials
Final material properties surpass MPIF-35 minimum specifications with excellent surface finish and feature resolution while the design freedom of additive manufacturing enables features like fully closed-cell gyroid infill for lightweight strength. 3D print complex metal parts in a variety of materials:
- 17-4 PH Stainless Steel
- 316L Stainless Steel
- 4140 Low-Alloy Steel
- A2
- Copper*
- D2 Tool Steel
- H13 Tool Steel
- Nickel Alloy IN625
- Titanium (Ti64)*
* Requires chemical debinder
Read Success Stories
Manufacturers and universities from across the globe are successfully using the Studio System. The office-friendly metal 3D printing systems is helping manufacturers produce metal 3D printed parts affordably while reducing lead times and offering their customers design freedoms. With the safe powderless operations, universities can easily add the Studio System to their classrooms or labs to ensure advanced manufacturing technologies are accessible to students to prepare them for the workforce. Read the case studies of Studio System customers.
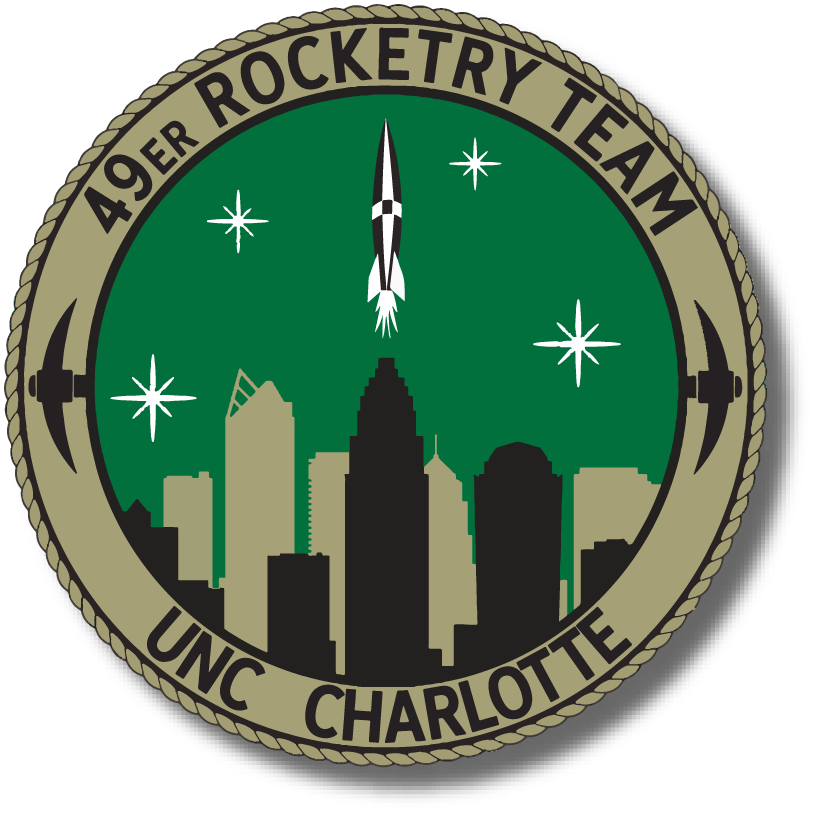
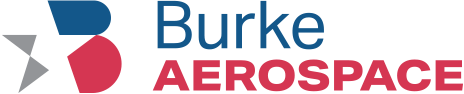
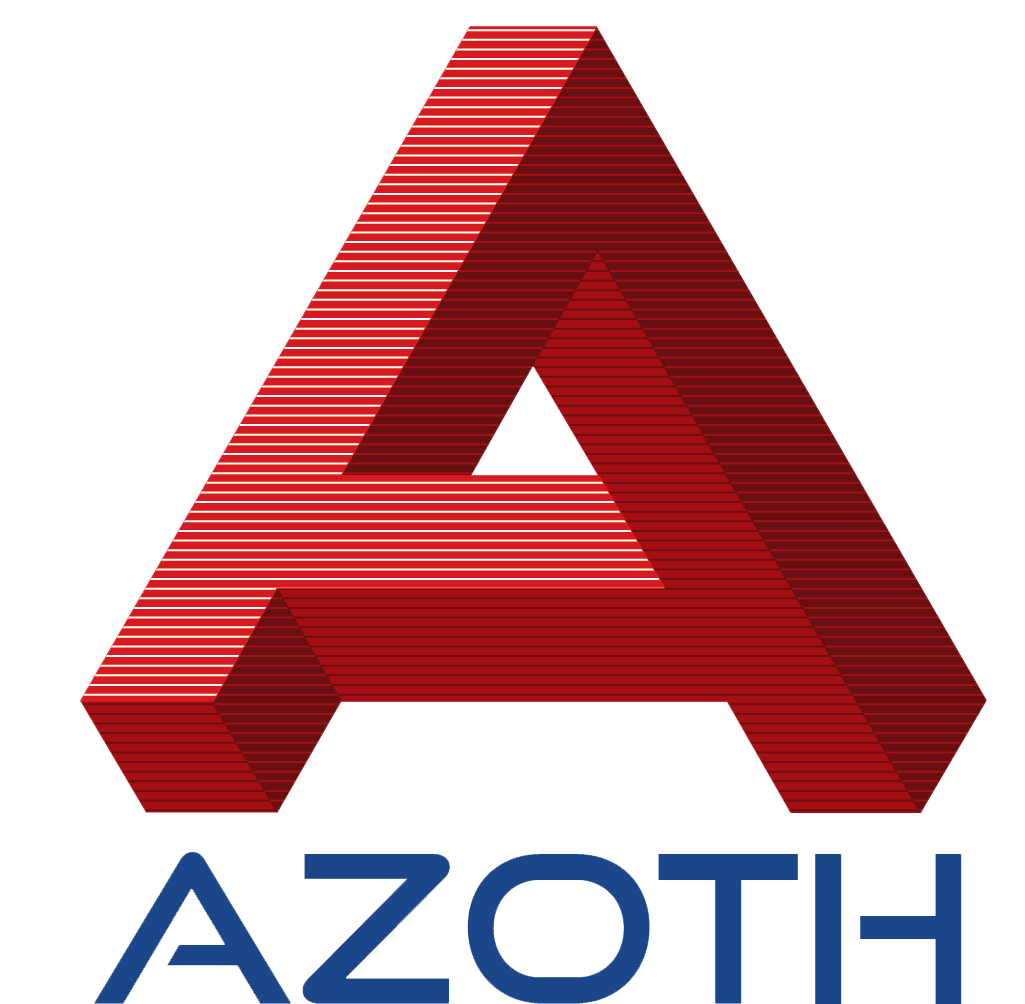
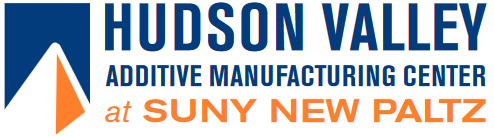
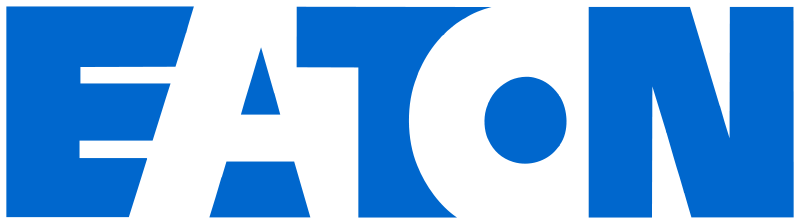
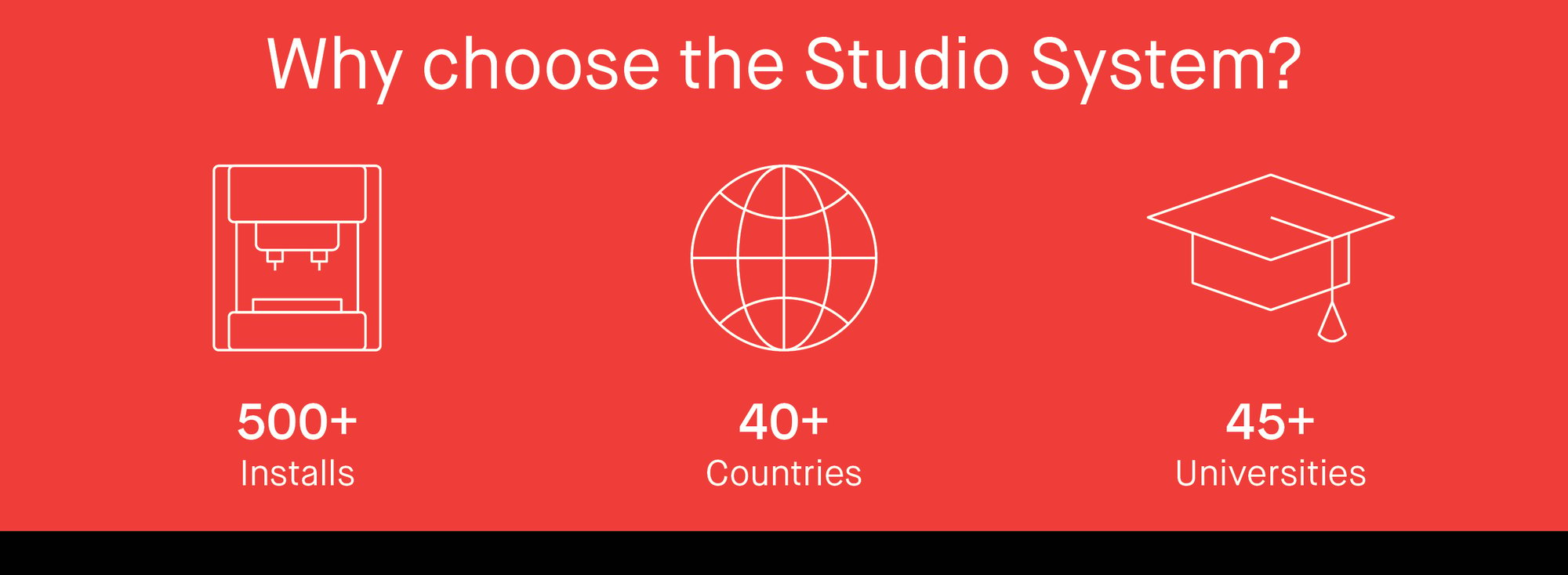